Table of contents:
- How EtherCAT works
- Brief description of the EtherCAT protocol
- EtherCAT network topology
- EtherCAT network redundancy and ring topology
- Precise time synchronization in EtherCAT
- Safety protocol (SIS) Safety over EtherCAT
- EtherCAT communication profiles
- Enterprise level communication via EtherCAT Automation Protocol (EAP)
- Application of EtherCAT in Digitization, Industry 4.0 and IoT
- EtherCAT equipment

EtherCAT is a high-performance Ethernet-based industrial communication protocol with support for various network topologies. It appeared in 2003, and since 2007 it has become an international standard. The protocol is being developed by the EtherCAT Technology Group.
How EtherCAT works
While in a conventional Ethernet network the master device uses separate commands to poll the slave devices, the EtherCAT protocol allows you to send only one command to poll and control several slave devices at once. Slave devices read the data they need fr om the Ethernet frame on the fly or write data for transmission and then forward the frame to the next device. This mechanism allows you to manage up to 65,535 devices in one network at high speed without restrictions in the network topology: line, bus, tree, star, or a combination of them. Moreover, to organize various topologies, hubs or switches are not needed, because. the slaves themselves have multiple ports. The process of communication with 1000 EtherCAT distributed digital I/O takes about 30 µs, which is typical for a 125 byte transfer at 100 Mbps. Data from 100 servo axes can be updated at up to 10 kHz.

The EtherCAT protocol can be used in both centralized and distributed automation systems. It supports master-to-slave, master-to-master and slave-to-slave modes, as well as integration with other industrial protocols. At the top level, you can apply the EtherCAT Automation Protocol, which allows you to work on the basis of an existing Ethernet infrastructure. In addition, EtherCAT allows real-time transmission of various protocols without affecting the transmission of process data. The Ethernet over EtherCAT profile allows you to encapsulate FTP, HTTP, TCP/IP, etc.
The EtherCAT protocol is based on Ethernet technology and the IEEE 802 specification. It uses the same Ethernet frames and physical layer, but additionally allows:
- Work in hard real-time mode with a deterministic response time
- Create many nodes, each of which handles a small number of I / O points
- Reduce equipment costs when creating a data transmission infrastructure
The initiator of sending the command can only be the master device. All other devices only process the request from the master and forward it further, which avoids unpredictable delays and ensures real-time data transfer.
Master devices use a standard Ethernet Media Access Controller (MAC) and do not need any special network cards, which allows you to implement master devices on any Ethernet-enabled hardware platform, regardless of its RTOS (English Real-Time Operating System - Operating System). real time system) and software. Slave devices use a dedicated EtherCAT Slave Controller (ESC) to process frames on the fly at the hardware level.
Brief description of the EtherCAT protocol
EtherCAT uses regular Ethernet frames for data transmission. The EtherCAT frame has ID 0x88A4 in the EtherType field. Since EtherCAT is optimized for fast cyclic transmission of small chunks of data, it does not use resource-intensive TCP/IP and UDP/IP protocol stacks.

If it is necessary to integrate EtherCAT into a common IT infrastructure, TCP/IP traffic can be tunneled through the mailbox mechanism without affecting real-time control process data.
During startup, the master device configures the slave devices and defines a list of their parameters. The amount of data from one network node can range from one bit to several kilobytes. An EtherCAT frame includes a header and several datagrams. The datagram header indicates the type of data access:
- read, write, or both
- access to a specific device via direct addressing or access to multiple devices via logical (implicit) addressing
In addition to cyclic polling, it is possible to send datagrams event-based (asynchronously).
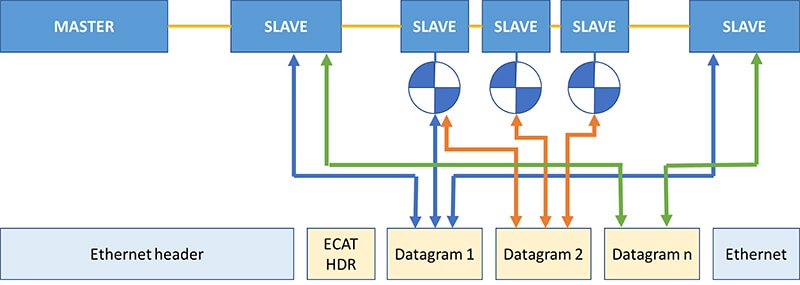
EtherCAT network topology
EtherCAT supports almost all existing network topologies: bus, tree, star or daisy-chain. Moreover, thousands of devices can be connected to EtherCAT without the use of switches and other intermediate equipment, which reduces costs and avoids restrictions when designing a network.
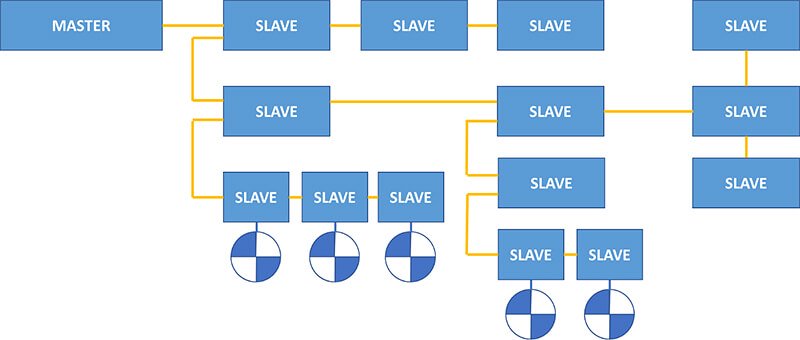
The logical topology of EtherCAT is a bus, but the physical connection can be anything. This is done because each EtherCAT device has multiple ports. It looks like this:
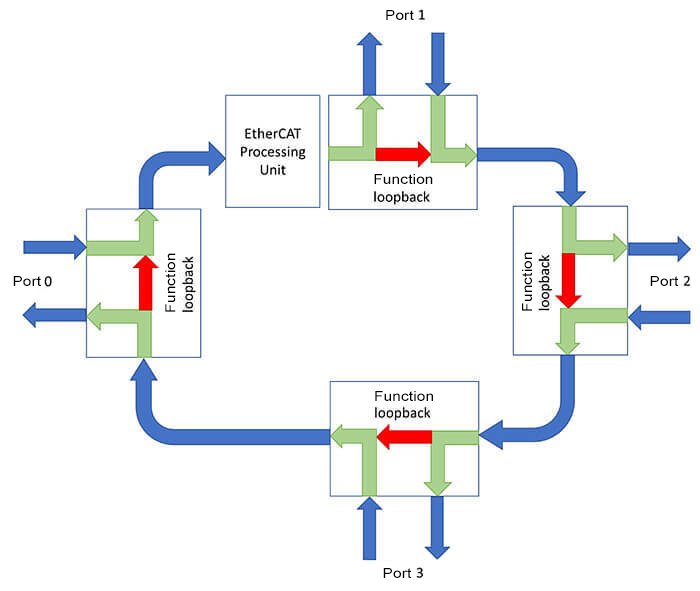
The master device sends a command to port 0 of the slave device, wh ere the command is processed on the fly by the EtherCAT Processing Unit and then forwarded to the next port. If the port is not connected to another device, then the command is forwarded unchanged to the next port until it returns to port 0 to the master device.
EtherCAT is compatible with standard Ethernet cables. For example, in standard 100BASE-TX mode, you can transfer data at a speed of 100 Mbps if the distance between devices does not exceed 100 m, and for data transmission over distances of more than 100 m, you can use optical fiber (100BASE-FX).
EtherCAT P (P means power) is an extension of the EtherCAT standard that allows both data and power to be transmitted over a single standard 4-wire Ethernet cable. This feature is useful when creating a bus of sensors with the organization of communication and power with just one cable. EtherCAT and EtherCAT P are identical in terms of protocol and differ only in the physical layer. EtherCAT P can be used on the same network as conventional EtherCAT devices. To convert EtherCAT to EtherCAT P and vice versa, special devices are used.
EtherCAT G/G10 is an extension of the EtherCAT standard that allows data transmission at 1 Gb/s or 10 Gb/s. This is especially true when transferring large amounts of data in machine vision tasks, fast measurement of parameters, or complex motion control applications. EtherCAT G/G10 supports all EtherCAT features and is fully compliant with the IEEE 802.3 standard. EtherCAT G adds the concept of branches to the standard, which is implemented using EtherCAT Branch Controllers (EBC) devices. EBCs are gateways between gigabit and megabit (100 Mbps) network segments, which makes it easy to integrate various types of networks into a single system.
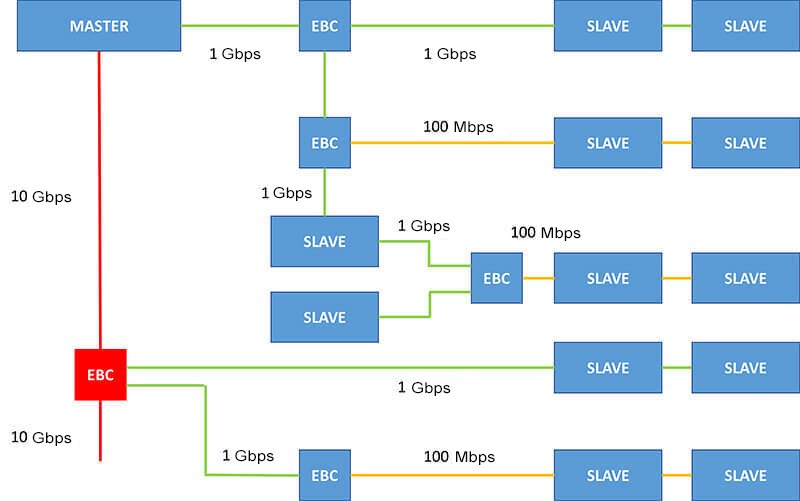
EtherCAT network redundancy and ring topology
A cable break or failure of one of the slave devices should not lead to the unavailability of the entire network or its segment, therefore EtherCAT has a built-in communication channel redundancy mechanism. The second Ethernet port of the last slave on the line is connected to the second Ethernet port of the master device, which allows the bus topology to be converted into a ring topology. A cable break or slave failure is detected on the master side. Slave devices do not require any modifications to work in the ring, because fr om their point of view this is no different from the normal EtherCAT operation.
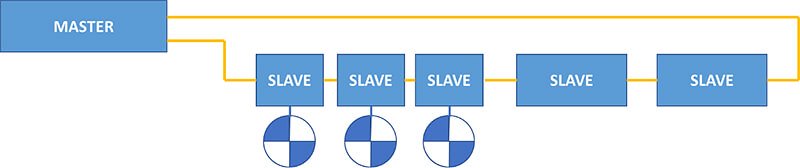
The network recovery time when a fault is detected does not exceed 15 microseconds, so a maximum of one polling cycle will be missed due to a fault. This means that even in motion control applications, a broken communication cable will not cause a process failure. EtherCAT also allows you to organize a hot standby for the master device. Potentially unreliable communication lines (for example, cable channels) can be connected not to the main, but to the EtherCAT drop line - then, in the event of a cable break, the rest of the system will continue to work as usual.
Precise time synchronization in EtherCAT
EtherCAT uses Distributed Clocks (DC) technology.

In an EtherCAT network, the time synchronization mechanism is implemented entirely in hardware. Clocks on slave devices can easily and accurately measure the delay relative to other clocks since the communication uses the logical and full duplex physical Ethernet ring structure, i.e. each EtherCAT packet travels twice through each slave (forward and return paths on different twisted pairs). Based on this delay value, the distributed clock is adjusted to achieve a very accurate time base with a spread well below 1 µs across the entire network.
Safety protocol (SIS) Safety over EtherCAT
Modern automation systems require not only time-determined transmission of control signals, but also the sending of critical information over the same communication channel. The EtherCAT standard uses the Safety over EtherCAT (FSoE - FailSafe over EtherCAT) protocol for this, which allows:
- use a single communication channel for the transmission of operational and critical data
- flexibly change and scale the architecture of the security system
- use already existing certified devices
- use advanced diagnostic tools for security devices
- seamlessly integrate the industrial safety system into the automation system
- use the same tools to create both regular systems and systems with increased reliability requirements
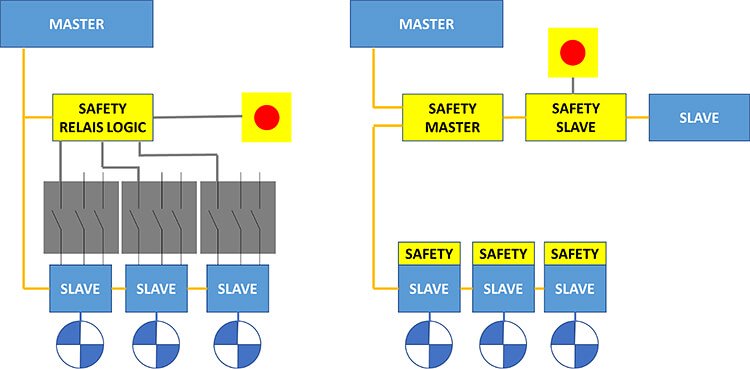
Safety over EtherCAT was developed according to the IEC 61508 standard, certified by TÜV and accepted as the IEC 61784-3 standard. The protocol is suitable for use in systems with functional safety requirements up to SIL4. Using Safety over EtherCAT allows the communication system to be considered part of a black channel that is not part of the safety system. Transmission of critical data and control signals is carried out via a single communication channel. Safety over EtherCAT protocol frames (also called safety containers) are transmitted over the network as part of an EtherCAT frame and contain critical data.
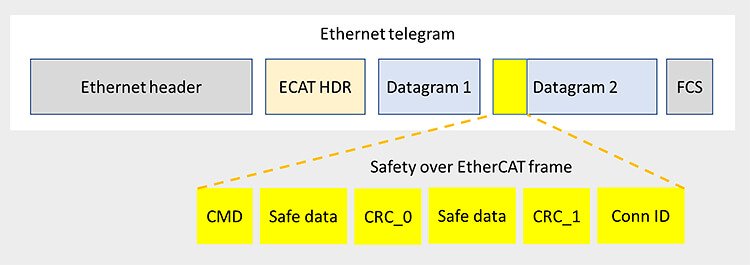
The use of Safety over EtherCAT simplifies the connection of various parts of the control system. The safety container passes through all slave devices, which makes it easy to organize an emergency stop of the entire equipment or its individual units - even if some of them are connected using a different protocol. FSoE support does not require significant hardware resources. The protocol provides high performance and low response time. For example, in robotics, FSoE is used in closed loop systems that operate at a frequency of 8 kHz.
EtherCAT communication profiles
EtherCAT supports acyclic access to variables, which can be useful for configuring and diagnosing slave devices. This mode uses mailbox technology with automatic recovery of damaged messages. EtherCAT supports multiple communication profiles:
- CAN application protocol over EtherCAT (CoE)
- Servo drive profile according to IEC 61800-7-204 (SoE)
- Ethernet over EtherCAT (EoE)
- File access over EtherCAT (FoE)
- ADS over EtherCAT (AoE)

Enterprise level communication via EtherCAT Automation Protocol (EAP)
The requirements for communication at the level of management of the entire production are slightly different from the requirements for communication at the field level. Quite often it is necessary to transfer information between individual plants and production lines. In addition, there is usually a central controller in the system that manages the production process on a global level, distributing tasks to individual production lines. EtherCAT Automation Protocol (EAP) can be used to interconnect different devices at the enterprise level.

The EAP protocol defines the following interfaces and services:
- data exchange between master devices
- data exchange with HMI (human-machine interface)
- traffic routing through EtherCAT protocol gateways to other industrial protocols
- integration of software for configuring devices and automation systems
The communication protocols included in EAP are part of the international IEC 61158 standard. EAP uses Ethernet as its physical layer - including wireless connectivity options - allowing it to be used in Automatically Guided Vehicles (AVG), which are often used in semiconductor manufacturing and in the automotive industry. industry.
EAP allows cyclic data exchange in push and poll modes. In push mode, each device sends data with a period equal to its cycle time (or a multiple of this time). Each device can subscribe to receive data only from certain devices. Senders and recipients are configured using the object dictionary. In poll mode, each device sends requests to other devices, and each of these devices responds to the request.
The cyclic exchange in EAP is based on the use of standard Ethernet frames with the identifier 0x88A4 in the EtherType field. This allows you to transfer frequently changing data with a millisecond cycle. If data transfer is required between devices located in different network segments, then TCP / IP or UDP / IP protocols can be used. In addition, EAP allows you to use the Safety over EtherCAT protocol for the transmission of critical data. It is commonly used in production line control systems wh ere individual control units need to exchange critical data for synchronous emergency shutdown or to relay messages to other lines in the event of a particular line shutdown.
Application of EtherCAT in Digitization, Industry 4.0 and IoT
EtherCAT meets the high demands of the Digitalization trend with its performance, flexibility and openness. EtherCAT can be used not only at the field level, but also used to connect to cloud services.
To connect to cloud services without having to reconfigure the master and slave devices, EtherCAT uses a communication gateway that can access all data by accessing the master's mailbox. The communication gateway can be a standalone device that communicates with the EtherCAT Master via TCP/IP or UDP/IP, or it can be an application on the master device itself. In addition, the openness of the protocol allows you to integrate IT protocols, such as: OPC UA, MQTT, AMQP and any others - either on the side of the master device, or directly on the slave devices, providing direct data transfer from sensors to the cloud service using a single protocol.
EtherCAT can work in TSN IEEE 802.1 (Time-Sensitive Networking) networks, which allows organizing exchange between controllers with real-time data transfer. In addition, EtherCAT supports integration with the OPC UA Pub-Sub protocol, which can be used for machine-to-machine (M2M) communication and communication with cloud services.
All of the above his allows us to say that EtherCAT is not just ready for Industry 4.0 and the Internet of Things (IoT), is already part of them!

EtherCAT equipment
Master devices
The Master device can be any device with a network card, because data processing on the fly occurs on specialized controllers in slave devices. The most common solution as a master device is the Beckhoff TwinCAT software installed on an industrial computer, or it can be a specialized controller. You can also use the software Open source implementation of the EtherCAT protocol. In addition, manufacturers of EtherCAT devices often supply various libraries and APIs with their products for self-implementation of the Master device.
PCIe EtherCAT Master cards
For a complete list of PCIe cards, see the catalog.

ECAT-M801-16AX - I/O module, 13 channels of digital I/O, simultaneous processing of up to 16 axes, 2-axis counter, EtherCAT Master

ECAT-M801-8AX/S - I/O module, 13 channels of digital I/O, simultaneous processing of up to 8 axes, 2-axis counter, EtherCAT Master, with DN-26 board, cables CA-1515M and CA-2615M
Controllers
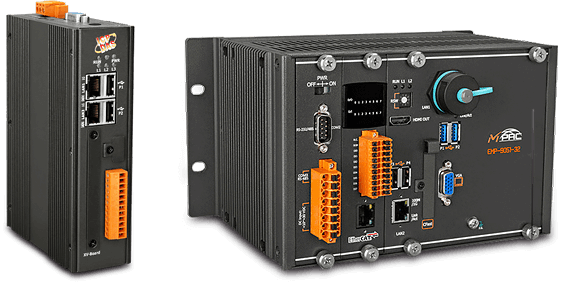
Model name | CPU | RAM, GB | I/O slots | Cycle time | Slave devices | Axles | Programming |
---|---|---|---|---|---|---|---|
EMP-9051-16 | i5-8365UE | 16 GB DDR4 | 0 | 500 µs, 1, 2, 4, 8 ms | 512 | 16 | С/С++/С#/LabView |
EMP-9051-32 | 32 | ||||||
EMP-9058-16 | 16 | IEC 61131-3 C/C++/C#/LabView | |||||
EMP-9058-32 | 32 | ||||||
EMP-9251-16 | 2 | 16 | С/С++/С#/LabView | ||||
EMP-9251-32 | 32 | ||||||
EMP-9258-16 | 16 | IEC 61131-3 C/C++/C#/LabView | |||||
EMP-9258-32 | 32 | IEC 61131-3 C/C++/C#/LabView | |||||
EMP-9091-16 | Atom E3950 | 8 GB DDR4 | 0 | 16 | С/С++/С#/LabView | ||
EMP-9091-32 | 32 | С/С++/С#/LabView | |||||
EMP-9098-16 | 16 | IEC 61131-3 C/C++/C#/LabView | |||||
EMP-9098-32 | 32 | IEC 61131-3 C/C++/C#/LabView | |||||
EMP-2848M | Cortex-A53 | 1 | 0 | 500 µs | 128 | 16 | IEC 61131-3 C/C++/C#/LabView |

Model name | CPU | RAM, GB | Modules | Programming |
---|---|---|---|---|
AMAX-5580-C300A | Celeron 3955U | 4 GB | AMAX-5000 series | CODESYS V3 Pure control |
AMAX-5580-54000A | i5-6300U | 8 GB | CODESYS V3 Motion | |
AMAX-5580-74000A | i7-6600U | CODESYS V3 Advanced motion |
I/O modules
For a complete list of I/O modules, see the catalog.

Protocol gateways
For more information about protocol gateways, see the catalog.

EtherCAT network topology converters
For more information about topology converters, see the catalog.

ECAT-2511-A - EtherCAT to single-mode fiber converter (WDM: TX 1310nm, RX 1550nm, SC connector, up to 25km)
ECAT-2511-B - EtherCAT to single-mode fiber converter (WDM: TX 1550nm, RX 1310nm, SC connector, up to 25km)

ECAT-2513 - EtherCAT bus junction module, 1 input and 3 bus output channels, EtherCAT Junction Slave

For further technical information, inquiries about offers or placement of orders, please contact our sales team at sales@ipc2u.com