Minimizing Hazardous Leaks in Vast Oil Refinery with ICP DAS ZigBee Wireless Solution
Industry 4.0, driven by the Industrial Internet of Things (IIoT), focuses on “Enhancing Industrial Safety through Smart Technology” nowadays. In this case study, ICP DAS demonstrates how using ZigBee wireless technology can provide a gas leak monitoring solution for Taiwan’s largest petroleum supplier. The solution overcomes the challenges arising from long distances across the vast plant and avoids hazards in the oil refinery.
The customer in this case owns three oil refineries operating to process crude oil and produce basic raw materials for the manufacture of petrochemicals. The total capacity of these refineries for crude oil can reach 720,000 barrels per day, which accounts for about 70% of Taiwan’s national oil supply. The following contents center around a plant located in Kaohsiung, Taiwan.
Vast Size of the Oil Refinery Poses Challenges for Gas Leak Detection
The oil refinery occupies a vast area of roughly 170 hectares, housing 26 large oil storage tanks of 6,000 cubic meters each, and 8 huge oil storage tanks of 50,000 cubic meters each. Monitoring numerous storage tanks simultaneously and transmitting all gas data back to the control center across the land is a significant challenge, requiring great wiring effort and cost. Besides, the issue of maximum wiring distances further complicates the situation.
Therefore, the customer chose the ICP DAS ZigBee gas detection solution. The characteristics of ZigBee wireless communication technology effectively address such problems and meet the requirements.
ICP DAS ZigBee Gas Detection Solution Offers Flexibility to Suit Existing Spaces
In this ICP DAS ZigBee wireless solution, the ZT-2017C ZigBee Current Input Module converts current signals—obtained from sensors installed in oil storage tanks—into readable digital values for gas concentrations. The data is then sent via ZigBee wireless communication to the ZT-2510 ZigBee Repeater to extend the reach of ZigBee signals, ensuring stable data transmission across the large-sized oil refinery. Later, the data is transmitted to the ZT-2570 ZigBee Converter and then to the control center via Ethernet. The SCADA performs gas concentration monitoring and alerts the staff to potential dangers. The system architecture is shown below.
Therefore, the customer chose the ICP DAS ZigBee gas detection solution. The characteristics of ZigBee wireless communication technology effectively address such problems and meet the requirements.
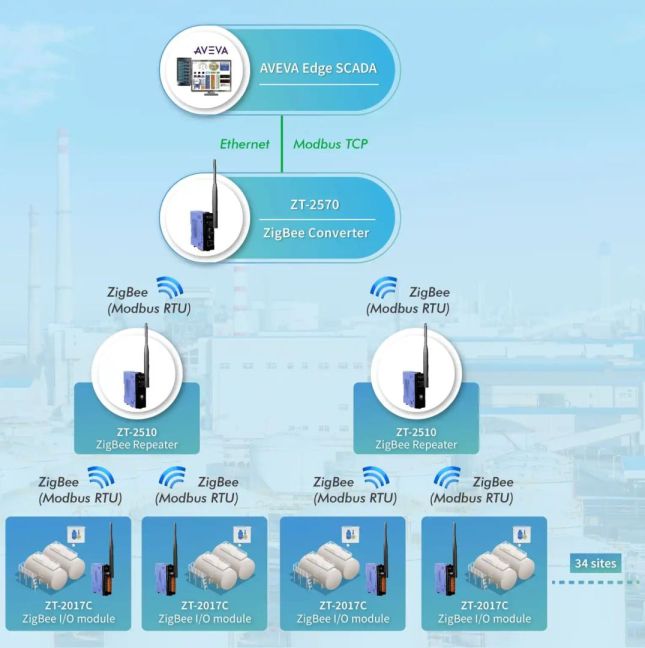
- ZigBee is an IEEE 802.15.4-based specification for wireless personal area networks (WPANs). The protocol specification is ideal for mid to long-range (10–700 meters) automation control and distributed control systems, characterized by its simplicity, strong anti-interference, low-cost, and high-security features.
- ZigBee network supports a large number of nodes and various network topologies, allowing messages to be transmitted using multi-hop mesh networking. In the event of a node failure, another node can take over from it and send the message to the destination device. The network ensures uninterrupted data transmission over long distances.
- ICP DAS ZT-2017C ZigBee Current Input Module is designed specifically to convert analog signals. The 8-channel analog input module can convert current signals into readable digital values for gas concentrations. Subsequently, the data is sent to the ZT-2510 ZigBee Repeater via ZigBee wireless communication.
- The ZT-2510 ZigBee Repeater can extend the ZigBee signal transmission distance and range, ensuring smooth communication over the mesh network despite the presence of obstacles. In this case, ZT-2510 extends the reach of ZigBee signals sent from the ZT-2017C ZigBee Current Input Module, addressing problems such as wiring difficulties and data transmission issues incurred by the vast size of the oil refinery.
- The ZT-2570 ZigBee Converter supports both Modbus RTU and Modbus TCP protocols. It can receive data via ZigBee wireless communication and then transmit data to the SCADA in the control center via Ethernet.
- AVEVA Edge is a comprehensive platform capable of developing full-featured HMI and SCADA applications with various fundamental tools provided. It can build powerful graphical user interfaces and includes standard features such as OPC UA and OPC Classic (HDA and DA), trends, alarms, reports, recipes, and built-in SQL database support. AVEVA Edge, with its strong integration and reporting capabilities, assists customers in collecting and analyzing big data. In this case, AVEVA Edge effectively monitors gas leak events in the oil refinery.
Enhance Oil Refinery Safety with ICP DAS Environmental Monitoring Solution
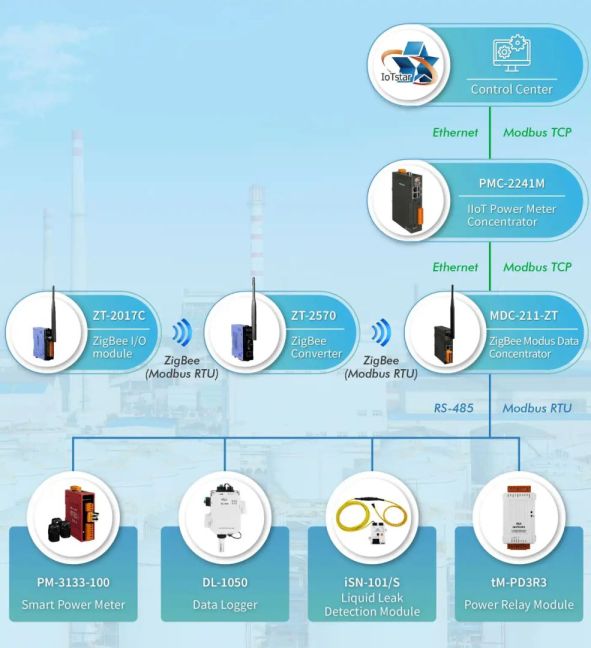
ICP DAS provides a holistic environmental and power monitoring solution that meets industry-specific needs. The products include PM series – smart power meters for power monitoring, DL-1000 Series – air quality data logger modules for air quality measurement, iSN series – liquid leakage detection modules for liquid leak event monitoring, and tM-PD3R3 Digital Input & Power Relay Module for access control. ICP DAS facilitates environmental and safety management of the plant.
- ICP DAS PM series – smart power meters are available in Modbus RTU/ Modbus TCP/ Ethernet/ CANopen versions, supporting multiple communication protocols. The series features high measurement accuracy (<0.5%, PF=1), and provides reliable energy consumption data, allowing users to monitor the energy consumption of the equipment in real-time.
- The DL-1000 Series – air quality data logger modules can measure O2, CO, CO2, HCHO, NH3, H2S, TVOC, PM1/2.5/10, temperature, and humidity. The series stores up to 180,000 records with date and time stamps. When the concentration of the gases and harmful particles exceeds the standard value, the series will raise the alarm.
- The DL-1000 series helps the customer detect the air quality and measure the H2S concentration in the oil refinery. Once the H2S concentration detected exceeds the preset upper threshold value, an alarm can be raised through the edge computing function of the ICP DAS Power Meter Concentrator (PMC) series to avoid harmful health effects or explosions caused by excessively high concentrations of H2S.
- The iSN series – liquid leakage detection modules work with CA-LLD-DC series – liquid leakage detection cables, enabling the detection of liquid leak events such as large-scale water leaks and leaks on water pipes. The modules then send the data back to the control center, keeping the right personnel posted on the leak events.
- tM-PD3R3 Digital Input & Power Relay Module transmits the data from the access control card readers to the PMC-2241M IIoT Power Meter Concentrator using Modbus RTU. PMC-2241M performs access control and it unlocks the door when the card reader allows one’s entry. Conversely, PMC-2241M sends an alarm notification to the management personnel when the card reader denies one’s entry. The system effectively helps the customer achieve access control of the plant for security purposes.
- The MDC-211-ZT ZigBee Modbus Data Concentrator features Ethernet, RS-232, RS-485, and ZigBee interfaces. It can upgrade the equipment originally using the Modbus RTU protocol to communicate using the Modbus TCP protocol. MDC-211-ZT combines the data read back from different slave devices into a continuous address format, allowing the host computer to read back the data of multiple slave devices at once. This is more time-saving as it replaces polling employed in the past.
- MDC-211-ZT can transmit data via ZigBee wireless communication, overcoming wiring difficulties in the field. In this case, MDC-211-ZT receives data on gas concentration as well as data sent from other equipment and devices using Modbus RTU.
- The PMC-2241M IIoT Power Meter Concentrator performs the functions of automatic logic control, remote monitoring, data collection, calculation, scheduling, and sending alarm notifications via emails and Line, etc. The built-in IF-THEN-ELSE statement enables alert messages to be sent based on pre-configured logic rules.
- PMC-2241M supports the data recovery function. In the event of network failure, the module still stores the sensor data in the built-in microSD card. When the network recovers, the module will transmit the stored data to the control center to avoid data loss.
- The IoTstar is an IIoT cloud management software developed by ICP DAS. It can remotely monitor, control, and manage IIoT controllers – WISE/PMC/PMD series, as well as I/O modules, devices, and equipment connected to the controllers. IoTstar also provides a web-based user interface with high convenience.
Moreover, users do not need to worry about the network environment of the on-site controllers. The management personnel can monitor controller status on the IoTstar no matter if the controller is assigned a static IP address, dynamic IP address, private IP address, or public IP address, thereby achieving multi-site environmental monitoring simultaneously. In addition, with IoTstar Dashboard Service, users can customize their dashboard based on their needs to monitor real-time data of equipment in the plant.
Conclusion:
Ensuring the safety of petrochemical plants is not only vital for industrial safety but is also intertwined with public safety and environmental concerns in the neighboring residential areas. A gas leak in the plant may cause air pollution and can easily trigger explosions. Besides, oil refineries house a large number of flammable and explosive substances that increase the risk of potential accidents, posing an immediate threat to workers’ lives and taking their toll on the health, safety, and lives of residents nearby.
“Safety” and “reliability” have been the core values of ICP DAS in product development for decades. The company is dedicated to developing new technologies and providing products that meet the specific requirements of each application based on field conditions. In the future, ICP DAS will continue to deliver tailored solutions focusing on environmental monitoring and safety.
Available models: