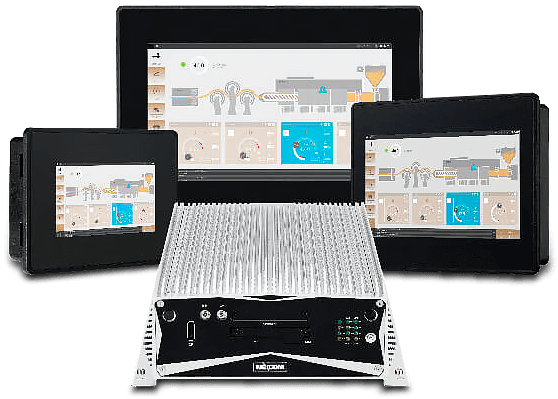
Project information
Task description: To build an industrial computer factory in line with the modern concept of Industry 4.0.
Client: NexAIoT subsidiary of Nexcom
Equipment used: Nexcom equipment, devices and solutions from other manufacturers and cloud service providers use is acceptable.
Project description
Nexcom company has spun off its subsidiary NexAIoT and built a Smart industrial computer factory. Industry 4.0 technologies allowed not only to monitor production in real time, but also to increase critical KPI by 15% - 25%. Nexcom is ready to share its experience in implementing Industry 4.0 technologies and offer a complex solution for digital transformation of production.
To combine information (IT) and operational technologies (OT) together, NexAIoT has developed the iAT2000 Cloud intelligent monitoring system. The cloud system made it possible to create a communication link between equipment and combine heterogeneous data.
System features
Cloud SCADA system iAT2000
- The automation system is based on high-performance PCs;
- Several systems are combined into one;
- An edge server is implemented for data preprocessing.
Real-time data processing and display in the control room
- 9 processes defining key KPI are configured;
- A system to display information on 8 monitors and a 16K video wall is configured;
- The information from various ERP, MES, SCADA systems is displayed.
Intelligent predictive maintenance system iPDM4.0
- A set of rules for production process managing is created;
- Real-time display of order status and cost is set up;
- Predictive equipment maintenance system is employed.
The NexAIoT Smart Factory system includes 9 systems, including IT ones: ERP/MES, iPDM4.0, information security system and 3D model of the plant; and OT systems: production systems, building management, power consumption, predictive analytics and Wi-Fi network.
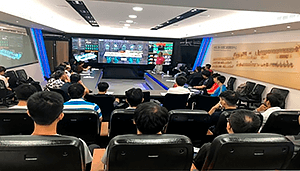
Smart factory control room
The cloud platform allows to display important information about all factory systems in real time and promptly make adjustments to the manufacturing line.
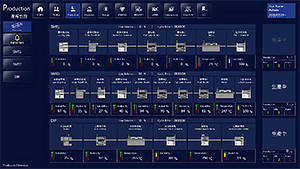
Production system
The iAT2000 platform united devices from different manufacturers with different communication protocols, which allows not only to monitor devices in real time, but also to quickly manage equipment.
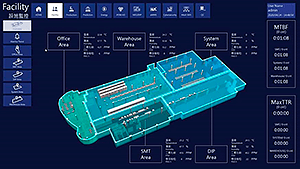
Building management system
The system collects data on temperature, humidity, and dust levels in rooms through sensors of the Internet of Things. Automatic adjustment of air conditioners and ventilation ensures comfortable working conditions for staff.
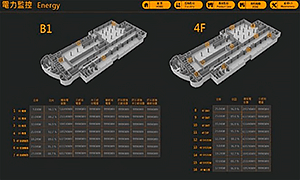
Energy management system
The iAT2000 monitors and records electricity, water, and air consumption. The data is then analyzed and used to optimize factory operations and reduce costs.
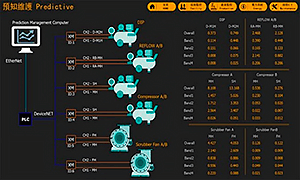
Predictive analytics
The cloud system monitors equipment operating time and conditions, such as: vibration level, temperature, humidity, and others. Special algorithms calculate optimal dates of equipment maintenance, which allows to increase equipment life time.
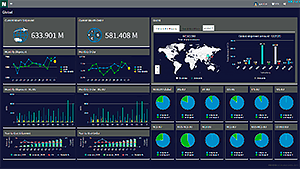
ERP and MES systems
In the unified iAT2000 system, various business processes are displayed: the company's revenue, the status of goods shipments, the estimated production capacity of the plant and other production parameters.
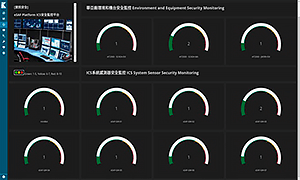
Information security
The system includes several levels of protection, both for production equipment and Cloud information systems of the company. Protection is carried out in real time through ICS intrusion detection systems and machine learning technologies.
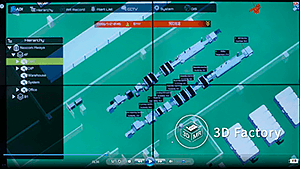
3D model of the factory
NexAIoT has created a 3D model of the factory for visualization of production and implementation of virtual and augmented reality technologies. Augmented reality glasses simplify remote diagnostics of faulty equipment.
Here is a video in which Jason, an automation project management specialist, talks about the equipment Nexcom used, the structure of the Smart Factory and what software was used.